Learn about the differences between annealed, tempered, and chemically strengthened glass. I explain each one and how it impacts the optical properties of glass, specifically first surface mirrors, beamsplitter mirrors, and anti-reflective glass.
Glass is used all around us in our everyday lives. Our cups, lightbulbs, car windows, phone screens, and even skyscrapers are composed of glass, but is it all the same? Glass is produced and treated in many ways depending on what it is going to be used for.
Let’s start by talking about annealed glass, also known as standard or float glass.
The term “annealed” is referring to the cooling process of the glass. Once limestone, soda ash, and several other things are melted at 2,700 degrees Fahrenheit, the liquid mixture is floated on a pool of molten tin. This is where the term “float glass” comes from!
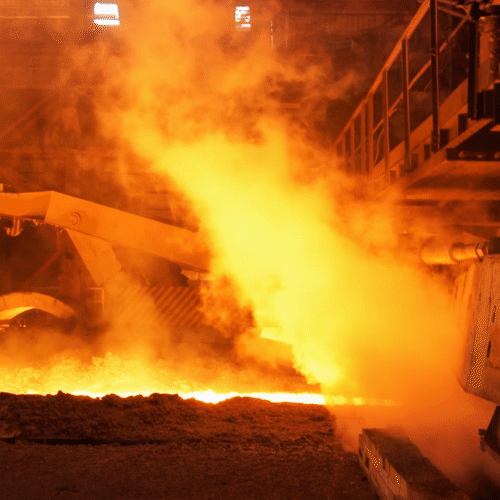
After this process, the glass is slowly cooled and stretched, which helps reduce internal stress that could cause breakage. When glass is annealed properly, it’s less prone to shattering or breaking. This being said though, annealed glass is thin and flexible enough that it can be cut, drilled, polished, or whatever else you may need to do to it without breaking.
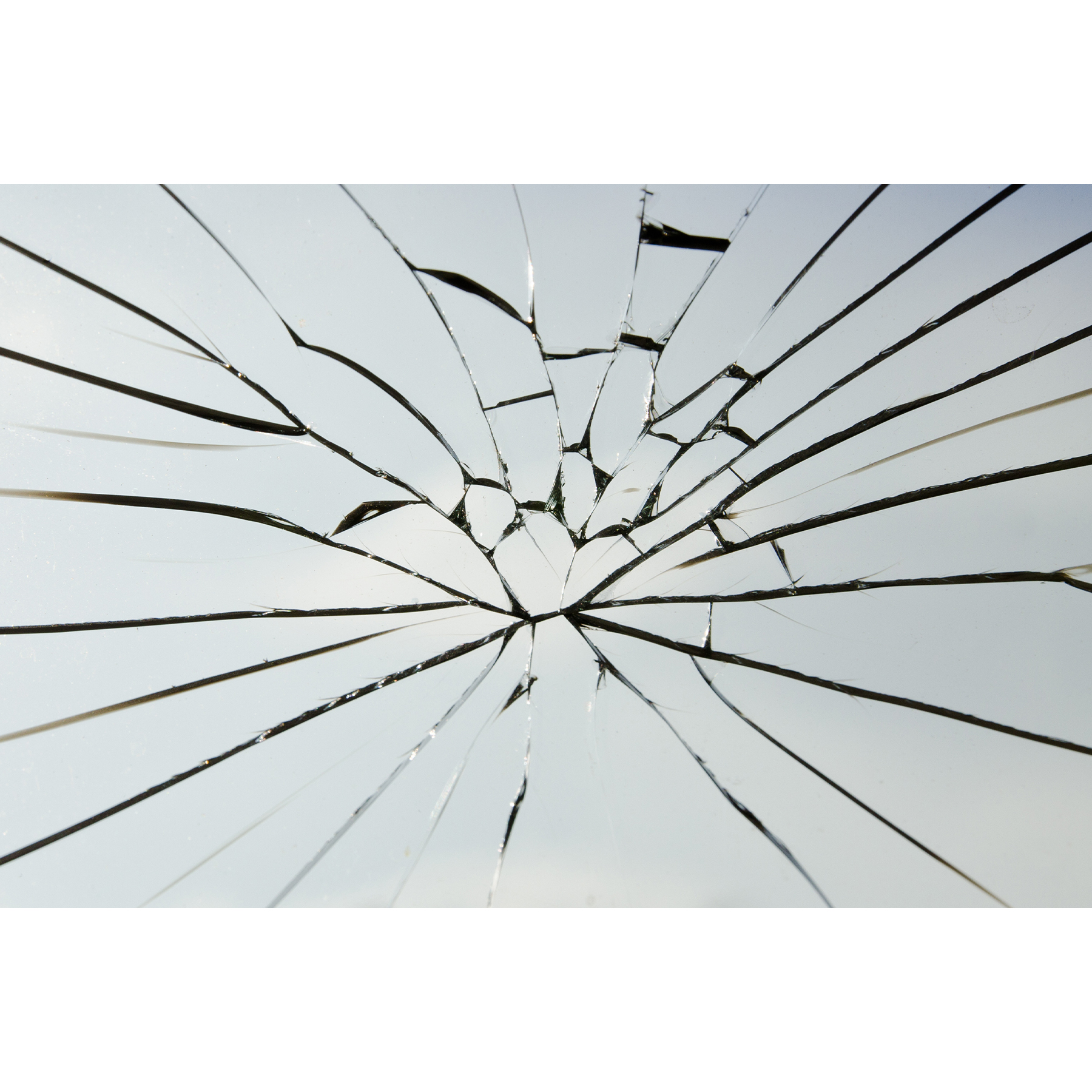
If annealed glass DOES break, it can shatter into long sharp pieces, which is why annealed glass isn’t known as safety glass. I’ll go over the benefits of tempering and laminating glass to improve safety.
With optical mirrors, both glass first surface mirrors and dielectric beamsplitter mirrors are typically supplied as annealed. They score and break just like standard glass and no further safety is needed. Annealed glass is extremely flat, which makes it ideal for making mirrors without distortion.
Next, we have tempered glass.
Tempered glass is most commonly used in car windows, shower doors, screen protectors for your smartphone, and is even a component in bulletproof glass. It is also known as safety glass.
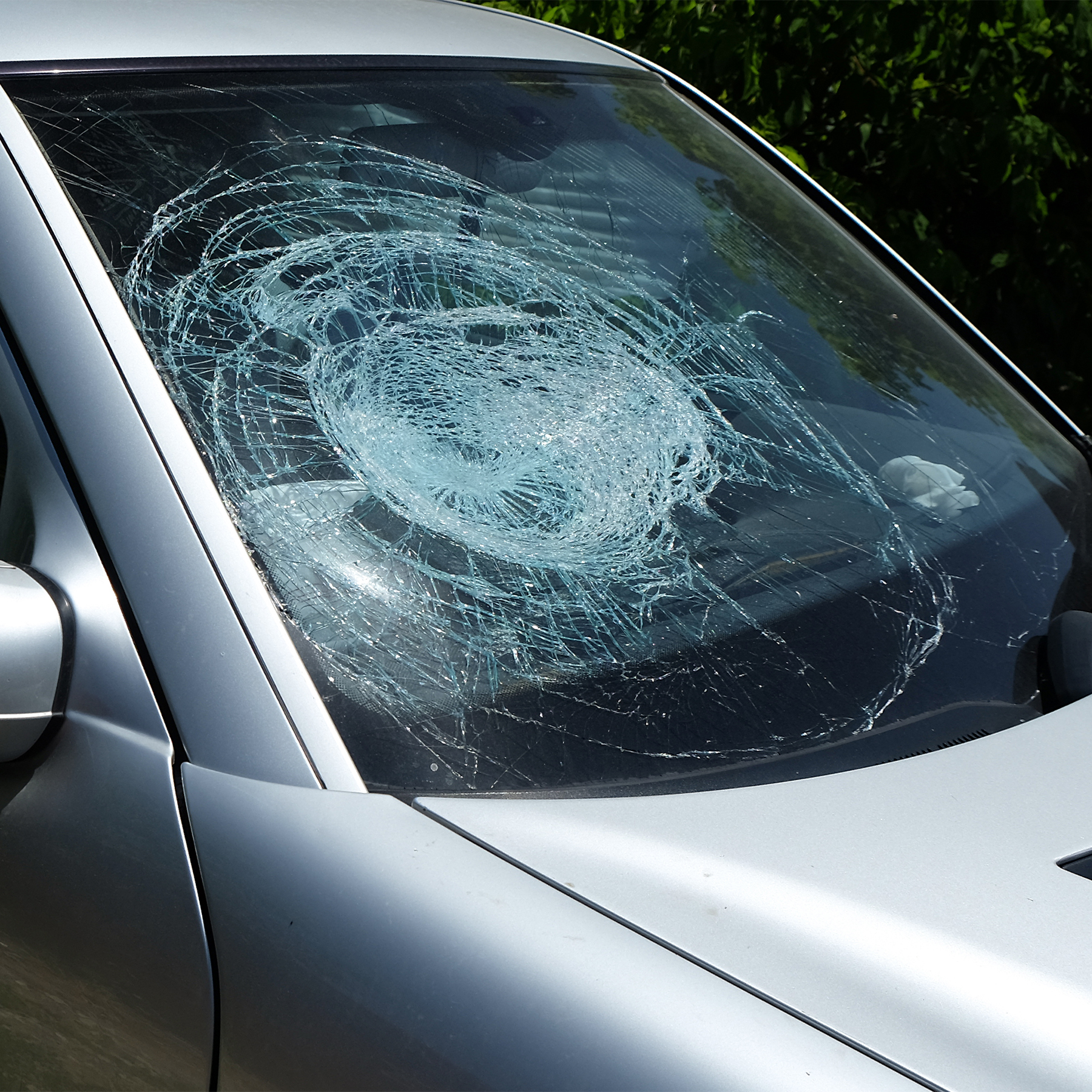
Tempered glass starts off as annealed glass. Before you put the glass into the furnace to be tempered, you need to cut down the glass to the exact size you need. Then it is put into a tempering furnace. At the end of the process, it is blasted with cool air in a process called quenching.
This causes the outer layer to cool quicker than the inner layer which causes tension within the glass, making it 10 times stronger. Because of the tension within the tempered glass, it cannot be cut or drilled without shattering it entirely. That is why you need to cut it to the size you need before tempering it.
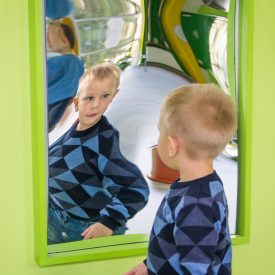
Generally, First Surface Mirrors are never supplied as tempered. This is because you need to apply the mirror coating before tempering and then once it is tempered, it can cause distortion which defeats the purpose of being an optically flat mirror.
That brings us to the main downside of tempered mirrors is the fact that the heating/cooling process can distort the reflection in the coating. That’s not an issue for anti-reflective glass, but can be more noticeable in glass with a higher reflection, such as beamsplitter glass.
It’s common for us to supply tempered anti-reflective glass and beamsplitter mirrors for applications where the optical properties are not as crucial as the safety factor. Anti-reflective glass is commonly used in science & engineering, museums, storefronts, display cases, architecture, and luxury homes.
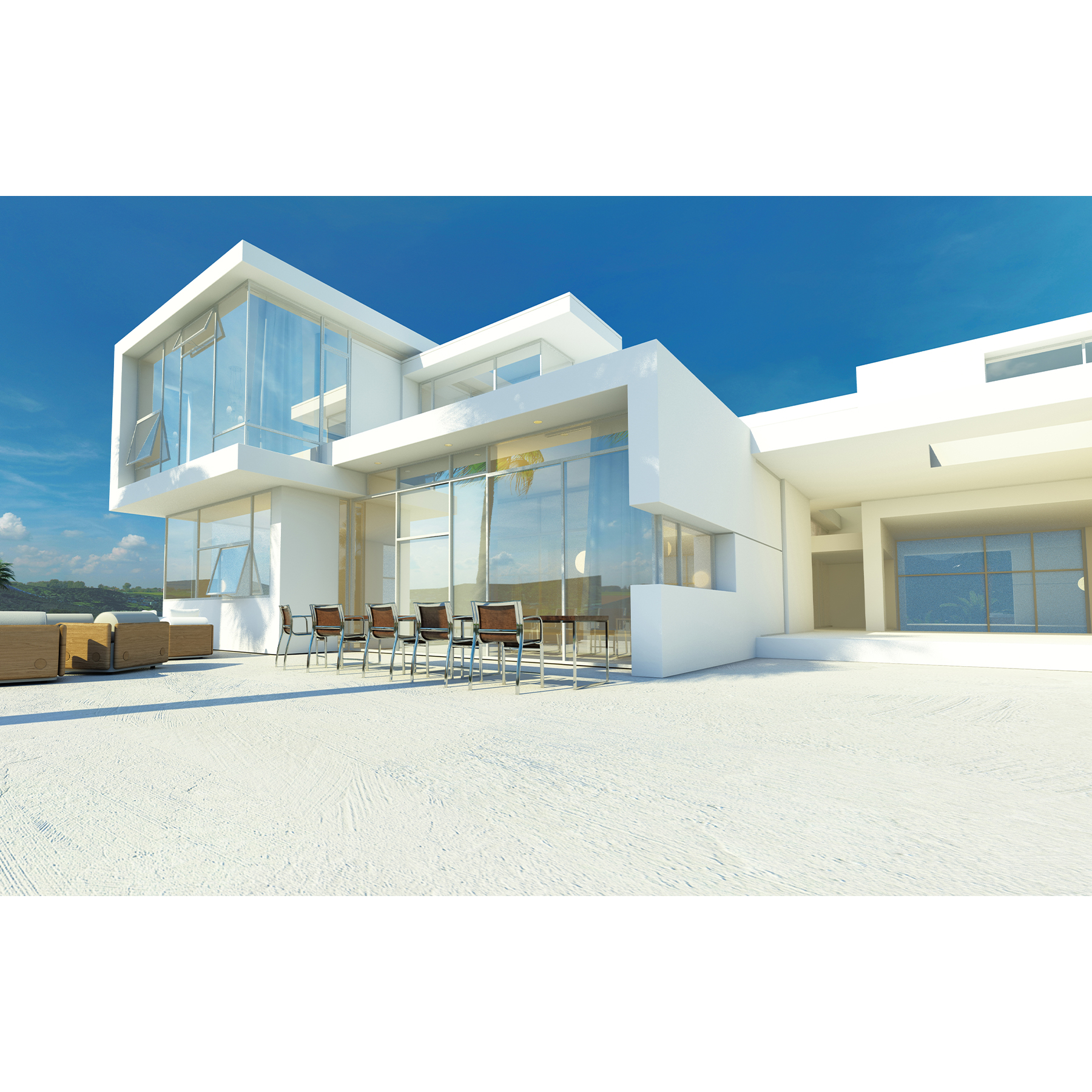
Tempered beamsplitter mirrors are used for digital signage mirrored displays, pepper’s ghost theater productions, and for mirror illusions in public spaces.
Last, but certainly not least, we have chemically strengthened glass

If tempered glass is already the stronger glass. . .what is chemically strengthened glass? Chemically strengthened glass is most commonly used for the screen of smartphones, photocopiers, and pharmaceutical devices. Certain car manufacturers are looking into using it for windshields as well.
Chemically strengthened glass also starts off as a standard glass, and then it undergoes a special molten salt bath. This process makes it 8 times stronger than your standard glass. This molten salt bath typically comprises of potassium nitrate at 450 degrees Celsius.
This causes potassium ions to replace the sodium ions in the glass. Potassium ions are larger than sodium ions, so when they squeeze into the gaps in the glass, it strengthens it. Pretty cool, right? Because the potassium ions are filling in the gaps, the glass is less likely to break.
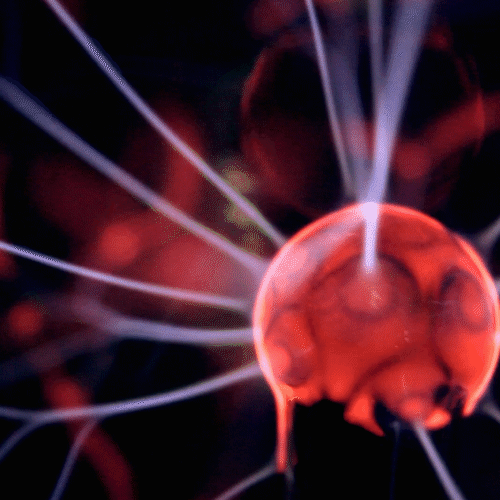
And the BEST part is, this process doesn’t warp or distort the glass like tempered glass so the reflection will still be crystal clear. That is why chemically strengthened Glass First Surface Mirror can be ideal for various applications. It preserves the optical qualities to provide an extremely accurate reflection while being stronger so the glass is way less likely to break. This is most commonly seen in systems with moving parts or chance of it breaking.
Cutting glass after this process is possible, but it will weaken the glass around the area where the cut was made. Chemical strengthening can also be done on thinner glass, where tempered glass needs a thicker cut because of the internal stress being put on the glass.
When you temper a 3mm thick mirror, it is super warped and still breaks easily. Depending on the shape it can also be bendy which is so weird to me! That is why we rarely supply tempered mirrors at 3mm thickness or thinner. While all glass has essentially the same starting process, there are many different treatments it can undergo depending on how it’s going to be used.
Hopefully this guide cleared up some questions you may have had, and if it didn’t drop a comment below and I’ll get back to you.